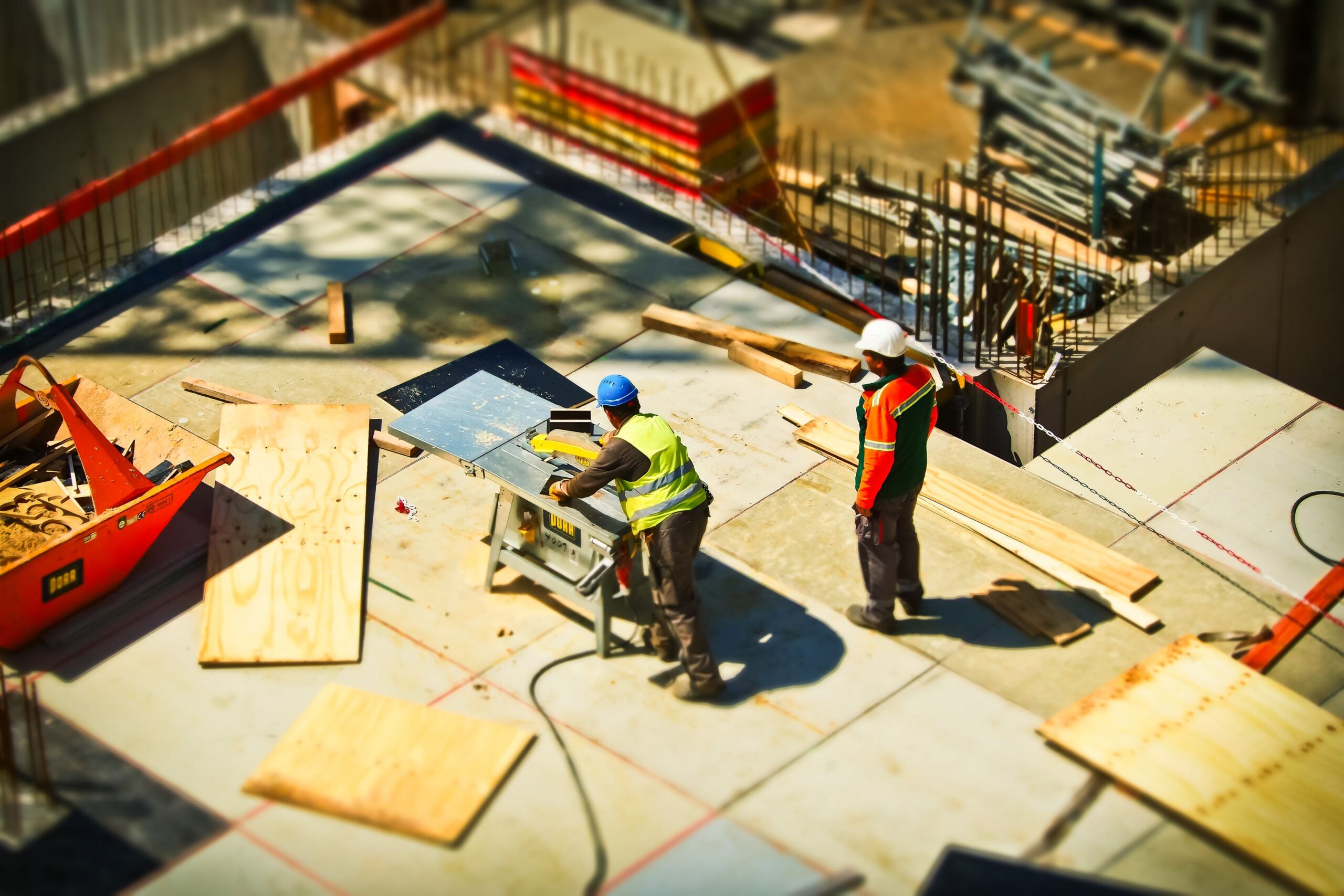
- Date: 17/02/2020
- Time: 06:40 AM
Why Use the MEP Design Build Delivery System?
Done properly, there is no better delivery method than design build to assure a smooth running project that delivers the best value to the owner. The key is ?done properly?. What does this mean? In a nutshell, it means professionalism and trust. The subcontractors must understand that design comes first, have experience in the process, have the owner?s interest at heart, and be trusted as a valued member of the team.
While there are still sectors that use the conventional design bid build process, they are generally limited more to the public sector or entities that have limited flexibility in purchasing practices. Colwill Engineering offers both pure design and design build. As such we have a rather unique perspective on both approaches. The differences can be illustrated by looking at the various phases of the project.
Design development is probably the most critical stage in setting the cost and benefits (value) of the project.? This is where various systems, materials, etc. should be evaluated to see what works best for the owner?s needs and budget.?
Reasons to Use a Design Build System
- The fact is that even the best engineering firms have limited knowledge of costs. Major equipment representatives (which represent major elements of project cost) will only provide engineers with the broadest idea of costs. Design builders on the other hand understand detailed costs. They have a history of previous purchases, and command the attention of the representatives who know they will ultimately be making the purchases.
- Pure engineering firms aren?t equipped to deal with the costs of various options in laying out the systems for a project. If anything, their thought process tends toward conservative design. It takes less time to do and creates less potential liability. A good design builder examines multiple system and layout options that will maximize use of standard equipment while still providing proper system operation and ample system capacity.?
- Comparison of systems and life cycle costing is more easily addressed by a design builder.
- The reasons are straightforward. As mentioned above, the design builder has better knowledge of costs, but they can also afford to spend more time.? Pure engineering fees generally dictate only being able to spend limited time in this type of analysis.
At the completion of design development, the differences in terms of project definition are dramatic. Using the design build approach the owner will have a lump sum price for doing things exactly as discussed and agreed in a written narrative during the process. Budgets can be finalized, and the decision making part of the project in terms of systems and quality is over. By comparison, in a design bid build scenario, the best that can be hoped for at this point is a rough subcontractor budget off preliminary documents, with no guarantee.
If the project winds up over budget (which happens more times than not), the process of value engineering starts, which is seldom beneficial to the owner. Contractors only offer as much in savings as they think is necessary to sell the project, and the engineers (who generally feel as though they already completed their work) are reluctant at best to make changes to the documents that have already been finished.
The volatility of commodities has not stopped. MEP pricing is dramatically affected by copper, aluminum, and steel. The design build approach allows the subcontractor to define requirements and make firm material commitments with suppliers immediately after design development and thus eliminate the issue of escalation.
The benefits of design build don?t stop with design development. They continue throughout the project.
Benefits of a Design Build System
- Ordering of long lead items is accomplished early on to assure there are no schedule issues.? This is very difficult to accomplish in design, bid, build.
- There is no ?shopping? of materials and the potential for dealing with submissions of supposed ?equal? products.? This is quite common in bid situations, particularly in today?s market where people can be particularly creative.
- While there has never been a perfect set of documents, there will be no change orders unless the scope of the project changes contrary to agreements made during design development.? Internal MEP coordination as well as coordination with other trades will be done during design and there are NO coordination change orders.? This is almost impossible to guarantee in design bid build.
- The RFI process is greatly abbreviated in design build.? The normal design bid build process requires paper work to make its way through a loop from subcontractor to general to architect to engineer and back again.? The process at best takes a few weeks, and generally the engineer?s answers are restricted by a fear of potential liability.? In design build, the decision is made with at most a few phone calls, properly documented, and the project proceeds.
To summarize, as said at the outset, done properly, there is no better delivery method than design build to assure a smooth running project that delivers the best value to the owner. The above examples illustrate why. The only key is to put the right people on the team.